Structural
SIP panels explained
Structural insulated panels (SIPs) are a wall system usually designed for residential or light commercial buildings. In a SIP insulation is sandwiched between two boards. The material of the board, as well as the insulation, differ between manufacturers. The sandwich material can be anything from plywood to magnesium boards.

SIPs are manufactured at the manufacturing site and specifically to the requirements of each building. SIPs often with windows, wiring and pipes. Some SIPs do not require any other cladding on the out- or inside, but can be clad.
The manufactured SIP wall sections are then transported to the site, where they are joined together to form your building.
The advantages of SIPs:
​
-
Faster built time as SIPs can be manufactured while the foundation work is carried out and it is faster to put up complete walls
-
Many SIPs outperform timber and steel frame construction for structural stability
The disadvantages of SIPs:
​
-
Many builders are unfamiliar with SIP building which leaves potential issues at the point where panels join with each other and cause water leaks
-
As often SIPs are delivered pre-wired and with electric socket outlets it is very difficult if you change your mind about power sockets and water pipes

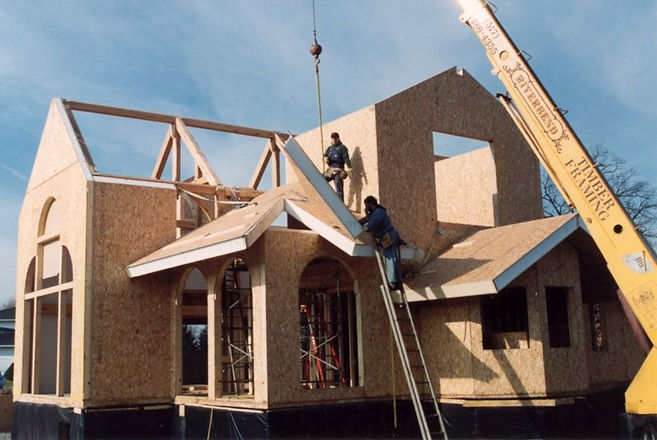
Environmental Impacts:
​
As the used materials in SIPs vary widely we are currently unable to give even an estimate on health or environmental impacts. Some are made of natural and or recycled materials that are good for the occupants and the planet, others are not. The importance in installing SIP panels is the joining of the wall sections, as those offer potential for water leaks. Sealants and covering boards are often used to ensure the building stays dry in the inside.